This new eBook discusses E-Power Resources’ strategic position within the graphite market, unravelling its distinctive business model, strategic alliances, and exploration endeavours.
E-Power Resources is developing essential graphite resources in Quebec for the EV battery factories already funded and under construction.
Amidst the transition towards clean energy, the demand for electric vehicles has surged, igniting a parallel increase in demand for graphite, a vital component in EV batteries.
In this transformation, E-Power Resources has emerged as a pivotal player, strategically positioned to capitalise on the burgeoning graphite market.
The company adopts a forward-thinking approach, focusing on securing graphite resources in their natural state rather than venturing into resource-intensive production processes.
By monetising graphite deposits while they remain in the ground, E-Power Resources optimises cost efficiency and minimises capital expenditure, positioning itself as a pivotal link in the burgeoning graphite supply chain.
Moreover, E-Power Resources’ strategic partnerships and geographical advantage further bolster its position in the market.
With flagship graphite properties strategically located in Quebec’s North Shore region, E-Power Resources enjoys unparalleled proximity to key transportation hubs, facilitating seamless access to North American and European battery production markets.
E-Power Resources is poised to redefine the graphite industry’s landscape and drive sustainable growth in the era of electric mobility.
What are the primary factors driving the demand for graphite? What are the current trends and dynamics operating within the graphite market?
Graphite is the largest material component of EV batteries. The typical EV battery has somewhere between 50-100 kilograms of graphite.
Graphite forms almost the entire anode side of the battery with silicon often being used as an additive at roughly 5% of the anode. The rest of the anode is all graphite.
The material composition of the cathode side, which contains the metals, often changes as different manufacturers rotate different metals in and out. Some batteries use metals not found in other batteries made by different producers.
On the anode side, there are, and have been, no material changes. They all use and need graphite. There is no known substitute.
The primary factor driving growth in graphite demand is the growth in battery production, especially EV batteries.
Additional EV battery manufacturing capacity is being erected all over North America and Europe. For example, Volkswagen announced several months ago that it is building a highly subsidised factory in St Thomas, Ontario, capable of making one million EV batteries per year and beginning production in 2028.
Toyota is building a factory in Liberty, North Carolina, with a budget of $13.9bn and is due to begin production in 2025. These are only two of many examples across North America and Europe.
According to Benchmark Mineral Intelligence, North American battery manufacturing capacity is estimated to be 17 times what it was in 2021 by 2035. This estimate was distributed in September 2022. I would not be surprised if it has been revised upward since then.
At 50 -100 kilograms of graphite per typical EV battery, procurement departments of manufacturers constructing huge factories worth billions of dollars are likely thinking ‘where will we get our graphite?’ Without graphite, they will not be producing any batteries.
For the moment, about half the graphite, or a bit less than half, going into EV batteries is synthetic.
One of the primary reasons for this is there is just not enough of the right natural graphite above ground to use in batteries, so manufacturers have taken the high-cost, high-environmental impact decision to use synthetic, even if they prefer to use natural.
There are two important reasons they would prefer natural to synthetic. Synthetic generally costs four to ten times the amount it costs to extract natural graphite from the ground. The other reason is the production of synthetic graphite requires a lot of fossil fuels and massive energy consumption.
Natural graphite begins as carbon-based life forms, like leaves, bushes, dead insects, etc. Over a long period of time (one million years), the Earth, through metamorphic events involving extreme heat and pressure, turned those carbon-based life forms into graphite.
In other words, the Earth cooked them at extremely high temperatures in a pressure cooker.
Synthetic graphite aims to duplicate that process by applying extreme heat and pressure to fossil fuels. The process starts with either petroleum coke, ironically a by-product of oil refineries, or coal tar, another fossil fuel, and applies extreme heat and pressure to them to simulate that metamorphic event that turned carbon-based life forms into graphite.
The result is synthetic graphite.
At 50 – 100 kilos of graphite required per typical EV battery; this means a lot of cooking!
Synthetic graphite works and is here to stay, and can be crafted for performance, but there is not enough production capacity of it to keep up with the growth in EV battery production.
Not to mention the massive environmental impact and required energy consumption to produce it. As manufacturers and governments strive to make EVs more affordable, synthetic cannot be the sole solution to the graphite shortage problem.
A lot more natural graphite, which the Earth has already cooked and pressurised a long time ago, is the obvious answer.
In 2022, World Mining Data reported that about 1.7 million tonnes of natural graphite were produced worldwide. About 67% of that came from China, followed by Mozambique (10%), Madagascar (7%), India (5%) and Brazil (5%). Those five countries, accounting for rounding, amount to 94% of global graphite production.
Four of those five countries are quite far away from the battery manufacturing plants being built across North America and Europe. The US has no graphite production! Canada has one producing mine, in Quebec, but it produces less than 1% of global graphite production.
In Europe, the situation is equally bleak. Norway produces less than 1% of the global supply, while Ukraine, Germany, and Austria collectively produce less than 1%. Turkey, not far from Europe, is the sixth largest producer, producing less than 2% of global production.
In any event, the world is not producing enough to satisfy the rapidly growing demand for EVs and fuel the expansion of the EV industry.
Compared to the 1.7 million tonnes of natural graphite produced in 2022, Benchmark Mineral Intelligence estimates that by 2035, 7.2 million tonnes of natural graphite will be necessary to meet global demand. That is less than 11 years from now!
In other words, the world needs about 97 new, world-class-sized graphite mines. My guess is that North America and Europe combined need at least 50 of those new mines to fuel their industries. Combine that with the fact that North America only has less than ten graphite resources of any significant size.
Bear in mind that the EV battery industry is not the only industry consuming graphite. Graphite is used by foundries in the steel industry and as a lubricant for machine parts.
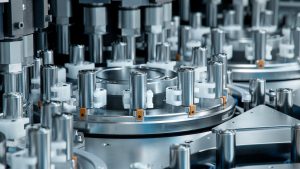
It is an additive to compounds to make them harder. Because it is so heat resistant, it is used in nuclear reactors. It is also a fire retardant. It can stand up to and hold molten metal. You will see it also in golf clubs and tennis racquets. Of course, we cannot forget the pencils!
One other emerging use of graphite is in batteries for power generation. Drive by a wind farm in Europe on a windy day, and you will often see that many of the turbines, if not all, are off.
They are off because if they are allowed to spin, they will overload the grid, so when it is windy, they turn them off, and when it is not, they use them!
After billions in subsidies have been granted to build these wind farms, politicians will want to show they were right to ensure their construction. One way to do that is to build gigantic batteries to store the power so that it can be released onto the grid at the right time. Showing they were right will surely merit a subsidy for those gigantic batteries.
As there is clearly not enough graphite above ground to go around, EV battery manufacturers will have to find ways to secure graphite while it is still in the ground to protect their massive investments in battery manufacturing capacity.
They are just beginning to realise this, as evidenced by the announcement of huge equity investments of over $150m USD in Nouveau Monde Graphite by General Motors, Panasonic, and Mitsui. This is the first time we have seen manufacturers begin to acquire large equity stakes in graphite resource companies.
This is probably a trend and is likely to accelerate as Nouveau Monde’s graphite is now effectively controlled by those industrial players and off the table for everyone else. There are only a few other graphite resource companies in North America from which to choose for all the other remaining industrial players.
E-Power Resources is one of those.
In what ways does E-Power Resources position itself within the graphite market in North America and Europe? How does the company use its strengths to operate effectively in these regions?
Our flagship graphite property is in the North Shore Region of Quebec, only about 3.5 hours drive from the Port of Baie-Comeau, at the mouth of the St Lawrence River.
We are very well-positioned geographically for both North American and European battery production.
Baie-Comeau has ground transport links to the rest of North America.
It has barge traffic all the way into the Great Lakes and is only about one week of sailing time away from Hamburg, Germany, for ocean-going vessels.
All but the last sixty kilometres of the journey are on a well-maintained highway meant to serve the iron mines further north and the hydroelectric power industry.
The last sixty kilometres of the trip are on Class 1 logging roads, which are not paved but engineered to handle large logging trucks for the vibrant timber industry in the area.
Our geographic position could not be much better.
What is your business model?
Our business model is focused on seizing one essential link in the battery supply chain in the least capital-intensive manner possible: graphite in the ground.
We differ from other North American companies in graphite resources because we do not intend to go into production ourselves, and we do not intend to become a battery anode material producer.
You will not see us coming to the capital markets looking to raise $200m for CAPEX.
Instead, we intend to monetise graphite while it still sits in the ground and repeat this process as often as possible. While Tetepisca, our flagship project, is one property, the potential to split it into several parts is there.
The graphite resources business has seen many companies drift downstream into manufacturing. We intend to stay upstream.
A few other graphite resource companies in North America, which started years before we did, have also delineated large, theoretical 43-101 graphite deposits in the ground.
However, the capital markets have not rewarded them for having these resources on the books, and their share prices remain rather low. Instead of going down the same path, we have chosen a different one.
Bay Street, Wall Street and the City of London seem to have forgotten the graphite resources business and do not yet understand graphite is crucial to EV battery production.
The capital markets abandoned us a long time ago, so instead of doing things to please them, like 43-101 resource estimates, we have embarked on a path to show manufacturers that our graphite will be useful to their production process.
In addition, we want to be able to show enough in-house resource estimates from various parts of the Tetepisca Property to illustrate the ability and potential to supply them with a lot of the right graphite to feed their manufacturing process.
We are not miners ourselves, but we can help discover and develop multiple graphite deposits on the Tetepisca Property and ultimately hand them over to manufacturers and their mining partners – for a price, of course.
Our business model can be summed up like this.
If you are going to spend $7bn on a factory, what is another $150m for a graphite deposit to ensure it can produce something?