Scientists from the University of Birmingham have discovered that ball milling provides high pressure effects during the manufacturing process for lithium-ion batteries.
Led by Dr Laura Driscoll, Dr Elizabeth Driscoll and Professor Peter Slater at the University of Birmingham, the team found that ball milling can cause high pressure effects on battery materials in just a matter of minutes.
The research, ‘Under Pressure: Offering Fundamental Insight into Structural Changes on Ball Milling Battery Materials,’ is part of the Faraday Institution funded CATMAT project.
The use of ball milling in lithium-ion battery production
Ball milling has seen a huge growth in being used to make next generation materials for lithium-ion batteries.
The process is simple and consists of milling powder compound with small bats that mix and make the particles smaller.
This creates high-capacity electrode materials, leading to more efficient lithium-ion batteries.
‘The discovery was almost an accident’
Previous research indicated that the synthesis of the electrode materials was caused by localised heating generated in the milling process.
However, researchers now have found that dynamic impacts from the ball milling colliding with the battery materials creates a pressure effect. This plays a huge role in causing the changes.
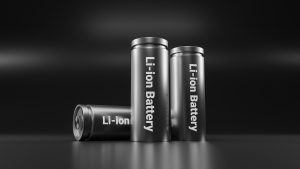
Peter Slater, Professor of Materials Chemistry and Co-Director of the Birmingham Centre for Energy Storage at the University of Birmingham, said: “This discovery was almost an accident. We ball milled lithium molybdate as a model system to explore oxygen redox in batteries, and noticed that there was a phase transformation to the high-pressure spinel polymorph, a specific crystal structure that has only previously been made under high-pressure conditions.
“Local heating alone could not explain this transformation. To test this theory, we then ball milled three other battery materials and our findings from these milling experiments reinforced our conclusion that local heating could not be the only reason for these changes.”
Applying heat would cause come compounds to return to their pre-milled state
The team found that applying heat would reverse the effects of the ball milling, showing that pressure was key in the original synthesis.
For example, production of the high-pressure spinel polymorph of Li2MoO4 was only previously achieved in a high temperature and high-pressure chamber under a pressure more than 10,000 times the pressure of Earth’s atmosphere.
In the wake of the new discovery, the same effect can now be found with just a few minutes of ball milling.
The discovery provides greater opportunities for the future
Co-author Dr Elizabeth Driscoll said: “This discovery provides the opportunity to develop cheaper, more energy efficient processes for battery manufacturers, and also to explore avenues for new materials. We found similar results, for example, when we ball milled disordered rocksalt phases which could be the key to producing better performing batteries.
“This improved understanding of the effect of ball milling on battery materials is incredibly exciting for researchers in this space, but also for the future of battery development as we were able to show that from five minutes of ball milling we could achieve the transformations that would usually require energy intensive and specialist equipment.
“As we move towards an increasingly electric future in order to limit pollution and reach net zero, it is vital that we continue to expand our knowledge and understanding of battery technology, so we can create the most efficient batteries possible. Our findings open the door to a world of new possibilities and discoveries and will hopefully play a part in a greener future for us all.”