Researchers from Chalmers University of Technology have developed a new battery recycling method that allows the recovery of 100% of the aluminium and 98% of the lithium in electric car batteries.
The new battery recycling method also minimises the loss of valuable materials such as nickel, cobalt, and manganese.
The researchers use oxalic acid to reduce costs and harmful chemicals in the process.
The paper, ‘Complete and selective recovery of lithium from EV lithium-ion batteries: Modelling and optimisation using oxalic acid as a leaching agent,’ is published in the journal Separation and Purification Technology.
How does the new battery recycling method work?
The team fine-tuned the temperature, concentration, and time to use the oxalic acid to facilitate EV battery recycling.
Martina Petranikova, Associate Professor at the Department of Chemistry and Chemical Engineering at Chalmers, said: “We need alternatives to inorganic chemicals. One of the biggest bottlenecks in today’s processes is removing residual materials like aluminium.
“This is an innovative method that can offer the recycling industry new alternatives and help solve problems that hinder development.”
The aqueous-based recycling method is called hydrometallurgy.
Traditional hydrometallurgy
In traditional hydrometallurgy, the metals in an EV battery cell are dissolved in an inorganic acid. The impurities, such as aluminium and copper, are then removed.
The valuable metals such as cobalt, manganese, lithium, and nickel are separately recovered.
Although the amount of residual copper and aluminium is small, several purification steps are required. Each step in this process can cause lithium to be lost.
The new method reduces the waste of valuable metals
The new battery recycling method reduces the waste of valuable metals needed to make new batteries by reversing the order of the traditional process. By doing this, lithium and aluminium are recovered first.
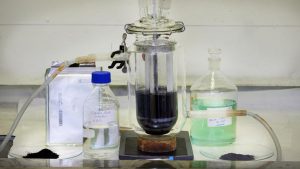
The latter part of the process leaves aluminium and lithium in the liquid, and the other metals in the solids. Aluminium and lithium then need to be separated.
“Since the metals have very different properties, we don’t think it’ll be hard to separate them. Our method is a promising new route for battery recycling – a route that definitely warrants further exploration,” said Léa Rouquette, PhD student at the Department of Chemistry and Chemical Engineering at Chalmers.
“As the method can be scaled up, we hope it can be used in industry in future years,” concluded Petranikova.