Determined to complete the battery value chain that is crucial to Canada’s net-zero future, BMAC is conducting an analysis of Canada’s critical minerals processing capabilities.
Determined to realise Canada’s net zero future, in 2022, the Battery Metals Association of Canada (BMAC) released a roadmap for Canada’s battery value chain. In collaboration with the Energy Futures Lab, Accelerate ZEV, and The Transition Accelerator, this roadmap presents a national strategy to enable Canada to leverage its abundant mineral resources while also driving its net-zero future. Critical materials go together with the green transition, with a thriving electric vehicle market necessitating an abundance of materials such as nickel, lithium, rare earths, and cobalt, to name a few.
Canada is rich in its quantity and variety of critical materials and could easily become a leading global supplier with the development of refining and production capacities. The roadmap is a comprehensive analysis of the Canadian battery supply chain and its potential, including specific timetables and targets for production, as well as a detailed action plan of the intricacies, challenges, and steps to be taken.
Direction of the roadmap
The action plan targets four goals, the first of which considers maximising the development and refining of Canada’s critical materials. This is a crucial aspect of Canada’s Critical Minerals strategy, aiming to improve access and increase supply by supporting the exploration of new projects, which can take up to 15 years, while also expanding the development of existing projects.
Goal two pertains to the chemical step of the battery supply chain, proposing the development of a world-leading processing industry. The third focus similarly considers the midstream of the battery production chain, evaluating Canada’s manufacturing potential and the opportunities to further engage in and improve production lines. Recognising the ever-increasing demand for batteries and new battery technologies, this is an area in which Canada, with its extensive innovative capabilities, could flourish.
The roadmap’s fourth and final goal is recycling and completing the battery supply chain. A truly sustainable battery chain requires the circularity of resources. BMAC’s roadmap discusses the value of establishing a closed-loop battery recycling industry that will enable Canada to sustain the supply chain – and the demand it intends to meet – in the long term.
Regarding all four goals, BMAC seeks to understand the realities of efficient and competitive implementation: The required investment, technological advances, and potential legislation. Such a comprehensive discussion highlights Canada’s potential to establish a successful, integrated battery supply chain that will attract foreign investment and foster innovation while striving towards a global net-zero economy.
The focus on Canada’s critical minerals processing capabilities
The roadmap concluded by presenting its findings, identifying and prioritising the next steps. One of the key findings was the need to develop mid-stream critical minerals processing capabilities that would address Canada’s current gap in the supply chain. For instance, lithium processing transforms the mineral extracted from spodumene and brines into battery-grade lithium.
Currently, the world’s lithium processing capabilities are dominated by Asia, requiring mined lithium to be exported for refining and processing before being imported for battery manufacture. The lack of domestic processing capacity in Canada is complicating the supply chain. With such a wealth of mineral resources, the logical next step is developing a world-leading chemical industry, therefore completing the supply chain from extraction to production. This will enable Canada to maximise its resources, support Canadian battery firms and create new export potential.
The analysis
In response to this finding, BMAC is now conducting an analysis of critical minerals processing capabilities in Canada. The aim is to identify the ideal methods to successfully implement material processing capacities in a globally competitive and preferably net-zero manner.
The analysis will focus on eight key materials: Lithium, nickel, copper, graphite, iron, phosphate, vanadium, and rare earth elements (REEs).
The eight key materials
There is a degree of uncertainty around which battery chemistries will dominate the market in the future. Those currently in use, like the nickel-rich higher energy batteries, require substantial amounts of nickel and cobalt, which are expensive to source. The move to lithium-iron-phosphate batteries in the electric vehicle industry is less costly but cannot provide the same energy density. Plenty of innovation is still required, and Canada can be best prepared by investigating a variety of materials that are likely to be employed in new applications.
For each of the chosen materials, BMAC has recruited specific industry experts to provide input on the ideal processing methods and technologies pertaining to the types and grades of the materials in Canada. Through a series of interactive online workshops, BMAC has engaged with expert feedback before utilising their knowledge through vetting the resultant flowsheets.
These critical materials will be evaluated against key questions to determine where and how would be most efficient and sustainable to process them.
What are the opportunities for Canada to process those critical materials?
A significant factor to consider is where there is active mining or exploring mining potential in Canada. Those places already in operation may be best placed for critical minerals processing possibilities, limiting the distance domestic materials travel for refining and processing.
Where are the optimal regions geographically to do it?
The criteria for identifying the optimal regions for processing capabilities have not yet been determined. Moreover, there is likely not a single set of criteria but multiple considerations that will vary between metals. However, each group of metals experts will provide a set of recommendations. This is only the beginning, as BMAC will also be doing follow-up work to further examine and define potential opportunities, specifically regarding the development of battery hubs in Western Canada.
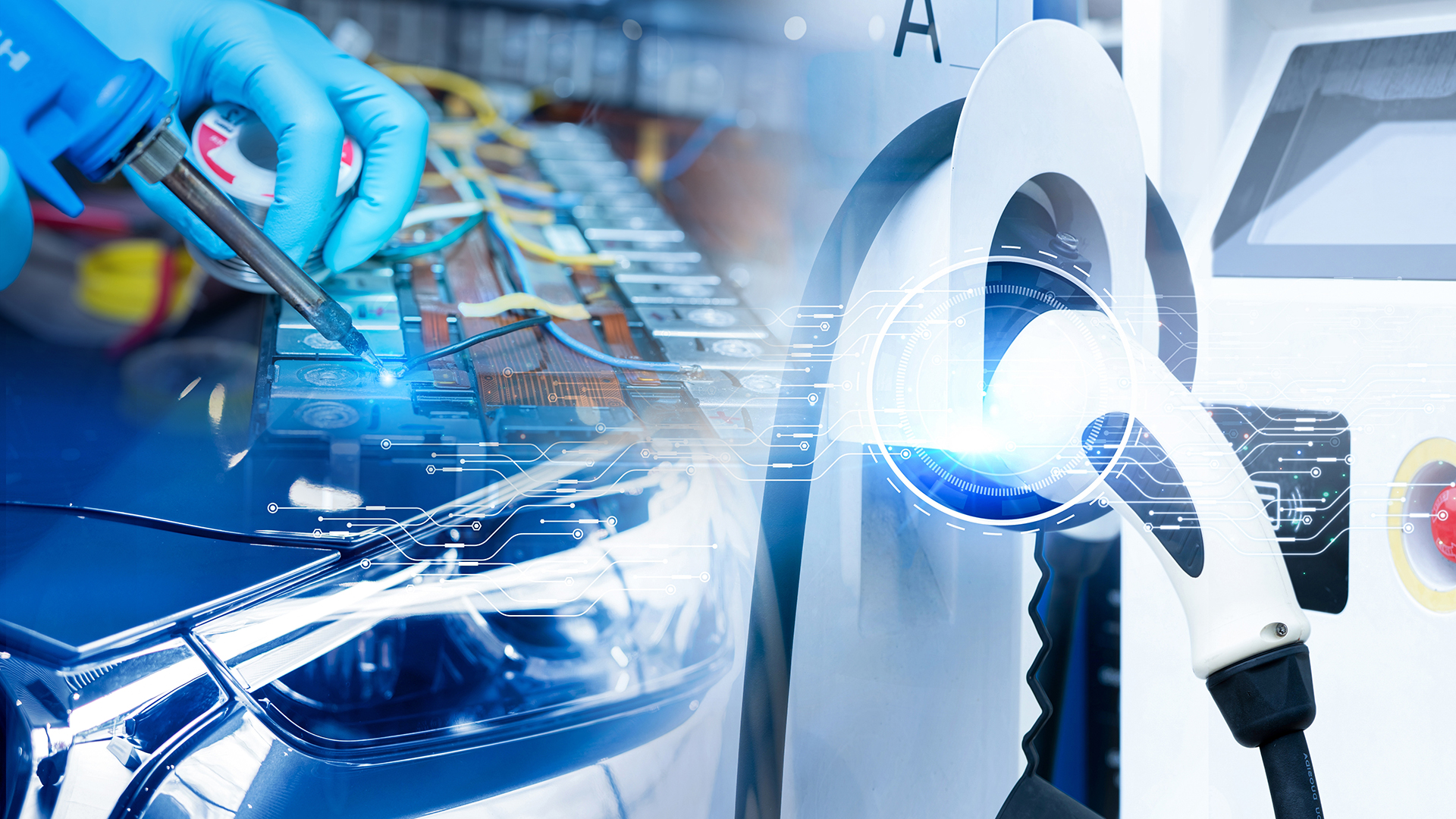
What are the least carbon-intensive approaches?
The roadmap aims to establish a competitive yet sustainable battery metals supply chain. Though crucial to our net-zero future, existing battery supply chains are carbon-intensive and detrimental to the environment. BMAC recognises that the future of battery supply chains lies with a reduction in carbon footprint and that strengthening Canada’s position in the global battery market should be conducted in a manner that will also secure its longevity. To achieve this, the analysis intends to address areas for improvement across the supply chain and identify strategies to mitigate the carbon intensity of processing each of the key materials, addressing areas such as technology, travel, and energy efficiency. In itself, developing critical minerals processing facilities in Canada would create a local supply chain, drastically reducing the carbon footprint of extracted metals that are exported for processing.
Separately, another project BMAC seeks to initiate involves ESG modelling and calculations for the Canadian value chain. These calculations have great complexity, so the analysis will begin by considering the carbon element. Eventually, this work could investigate the other potential impacts of developing processing facilities, including the ramifications on local communities, the economy and future legislation.
What is the ideal flow of the materials from extraction to production?
Consideration of the ideal flow of materials is a crucial part of every production and co-ordination process, referring to the efficient movement of materials throughout the entire supply chain. Essentially, ideal flow equals the lowest impact yet most competitive design, avoiding delays, reducing costs, and increasing efficiency. This will strive to discover the solutions with the lowest environmental impact – working towards the net zero goal and proving the most cost-effective and efficient.
Each material has unique aspects that require it to be addressed individually and comprehensively – as is most easily demonstrated by Canada’s lithium deposits.
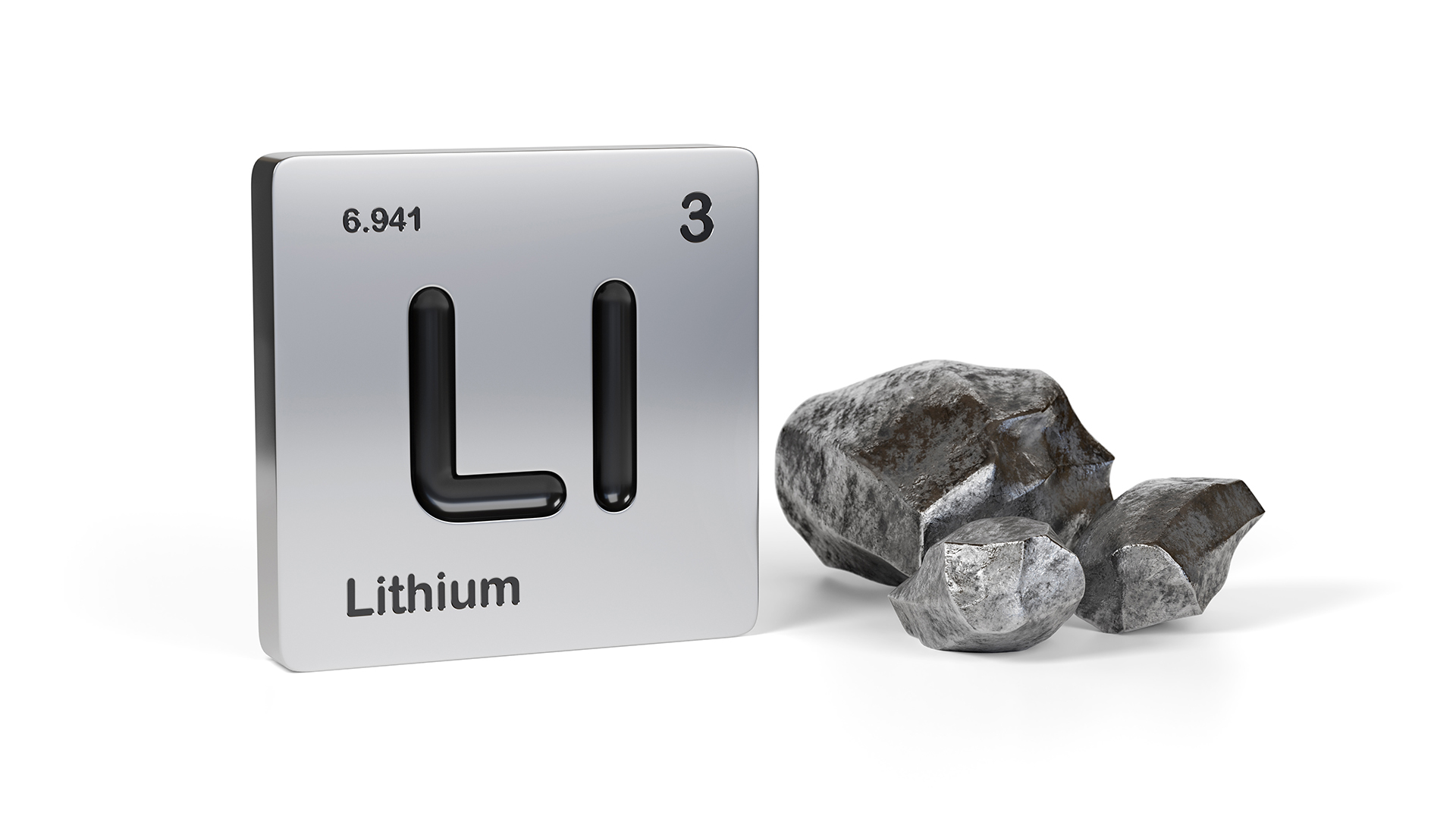
Canada has significant lithium resources in the form of both spodumene and brine. The east is home to primarily hard rock spodumene deposits, which are mined before undergoing leaching and purification to produce battery-grade lithium. In the West, brine-based lithium resources hold lithium dissolved in water. Direct lithium extraction (DLE) is revolutionising the brine-based lithium industry, and a variety of startups are positioned to mass-produce lithium by 2025-2027.
Consequently, in its analysis of lithium, BMAC’s work is intended to address the development of these two completely disparate processes. Flowsheets for both hard rock and brine-based lithium will be produced since the supply from both will likely be necessary in order to meet increasing demand. Therefore, the report will not recommend one source over the other, but instead, it will identify whether one is more suitable than the other for specific processes.
Outcome
The roadmap wanted to address what was required to both replicate Canada’s existing 10% share of the North American automotive market and meet the government mandate of 100% ZEV light-duty vehicles by 2035. Developing Canada’s critical minerals processing capabilities is crucial for achieving these goals, as well as for enabling a sustainable value chain.
It is difficult to determine a specific timeline for completing a local value chain in Canada. Several unknown factors are responsible for this, primarily that we do not yet know the battery chemistries Canada will produce and, therefore, the demand for the relevant materials. Arguably, the value chain does not need to be wholly completed for all key materials, as there is likely to be cross-border collaboration in the production of EVs across North America.
BMAC’s metals strategies will identify the opportunities for developing Canada’s mid-stream processing capacities, identifying key regions and ideal processes that can be implemented to bridge the gap, and take materials from extraction through production.
The analysis hopes to provide comprehensive flowsheets that can direct Canada’s battery value chain. BMAC anticipates these strategies will be released around mid-2024, with the follow-up work of the value chain opportunities for Western Canada completed by the end of the year.
Please note, this article will also appear in the seventeenth edition of our quarterly publication.