The FlowPhotoChem Project is helping to achieve European climate targets by delivering innovations for sustainable chemical production.
The EU has committed to tackling climate change targets head-on, aiming to reduce CO2 by 40% by 2030 and achieve a climate-neutral economy by 2050.
The European chemical industry, one of the largest manufacturing sectors and producers of high-value industry-wide materials, must also significantly reduce carbon emissions to meet these targets.
Europe’s chemical sector is one of the most polluting industries, with figures estimating that the sector released 123 million tons of CO2 equivalents in 2021. This is because a significant portion of chemical production is derived from fossil fuels, using processes that also generate significant quantities of greenhouse gases.
Launched in June 2020, FlowPhotoChem is a 48-month Horizon 2020 project that aims to make Europe’s chemical industry more sustainable by focusing on sustainable approaches to manufacture ethylene – a chemical used in producing plastic polyethylene. FlowPhotoChem will not produce CO2; instead, it will consume CO2 during the process.
Developing three types of reactors for sustainable chemical production
The FlowPhotoChem project has made strides in developing a novel modular system of flow reactors for the use of carbon dioxide in chemical production, providing new technology with the potential to help meet CO2 reduction targets.
The team has yielded significant achievements with three types of reactors associated with reducing CO2, upping their efficiency, and lowering their cost. The modular flow reactors – photoelectrochemical (PEC), photocatalytic (PC), and electrochemical (EC) – each operate in a unique way.
Why modular? FlowPhotoChem’s modular reactor technology allows for the production of a broader range of chemicals compared to dedicated non-modular systems because different combinations of reactors (PEC, PC, and EC) can overcome kinetic barriers and thus lead to a variety of final chemicals. While multiple reactors are more expensive than a single dedicated reactor, the extra costs are worthwhile since the reactions and reactors can be optimised for each end product with higher efficiency and stability.
Photoelectrochemical reactor
By using solar energy, FlowPhotoChem’s photoelectrochemical (PEC) reactor converts water into hydrogen and oxygen, while adding CO2 into the process can also produce solar syngas and other chemicals.
Previously, these technologies and types of reactions have relied on unstable catalytic materials, meaning that costs and stability needed to be improved. However, this new advancement utilises methods that will allow for a more straightforward reduction of CO2 as well as storage of solar energy.
The partners used computer modelling to design optimised catalysts that have a high yield efficiency and long-term stability.
By using more concentrated sunlight, the efficiency of solar-to-CO2 is raised to 19%. This demonstrates a viable method of converting CO2 with sunlight and represents a way to reduce CO2 while using sustainable energy.
It is intended that the excess heat produced from this chemical reaction can then be used to feed the photo-catalytic (PC) reactor.
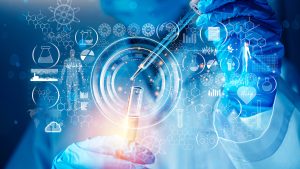
Photocatalytic reactor
A photocatalytic (PC) reactor uses light energy and a catalyst to drive a chemical reaction. FlowPhotoChem researchers utilise the PC reactor to combine CO2 with the hydrogen produced from the PEC reactor to produce CO and the base material for plastics.
Incorporating a co-doped hydroxyapatite (HAP) catalyst significantly improved the rate of combining CO2 with H2, a process known as hydrogenation. With the HAP catalyst in place, conversion rates increased- as high as 21.4%.
Moreover, there is a further improvement when both visible and near-infrared light are used. This is an advantage, as it reduces the rate at which solar energy is wasted during the process, helping to contribute to sustainable chemical production.
FlowPhotoChem researchers have developed a different type of PC reactor for alternative chemical reactions. This is based on a rotary system that uses continuously flowing material through the process, allowing for a consistent supply of the reagent mixture for conversion, and no clogging occurring.
Work has been undertaken on the use of continuous-flow photochemistry within photocatalytic reactors to assist with chemical production, including working on the efficiency of charge separation and slowing down the recombination kinetics to tackle the issue of light-to-chemical efficiency, and engineering the band gap of semiconductor photocatalysts to absorb visible light more efficiently.
Due to the nature of photochemistry, it has been difficult to perform on a large scale, because of the large amount of solid material required. But with FlowPhotoChem’s innovations, the process demonstrates extremely high CO selectivity due the careful design of the photocatalyst, reactor geometry and optimum operating conditions, improved conversion and formation rates, and enhanced stability of the catalysts involved.
Electrochemical reactor
An electrochemical reactor uses renewable energy and catalysts to convert the CO from the PC reactor into value-added products, including ethylene, ethanol, acetate, and n-propanol – the final stage of the chemical production process.
The FlowPhotoChem team has developed two distinct electrochemical reactors, a zero-gap lab-scale electrolyser and a 3D-printed reactor, both of which possess anodic and cathodic sides with corresponding catalysts.
The zero-gap electrolyser can effectively measure the ability of the electrochemical test cell, making the evolution of the reactor’s operation much more straightforward to study, and allowing the more accessible monitoring of degradation and deactivation pathways.
The 3D-printed reactor processes are simulated in a computer model, which can help to identify the most significant issues in developing an electrolyser cell and making it more productive.
Results and plans for the future
FlowPhotoChem culminates in 2024. The end result will be an end-to-end integrated demonstrator for solar ethylene production from water and CO2. The system is comprised of the three reactor types working together to create a continuous flow, ultimately producing ethylene.
Beyond that, a final report will be prepared with the closure of the project, and the next steps will be identified.
So far, all of the due milestones have been achieved, and the devices developed by other partners have been sent to our partner, Deutsches Zentrum für Luft- und Raumfahrt e.V., (DLR) in Germany, for work on an integrated demonstrator. The future is looking bright for sustainable chemical production facilitated by FlowPhotoChem.
This project has received funding from the European Union’s Horizon 2020 research and innovation programme under grant agreement No 862453. The material presented and views expressed here are the responsibilities of the author(s) only. The EU Commission takes no responsibility for any use made of the information set out.
Please note, this article will also appear in the seventeenth edition of our quarterly publication.