Neeraj Sharma, Director of the Australian Battery Society, alongside society member Clelia Nelson, discusses the issues surrounding supply chains, manufacturing, and recycling approaches in Australia for various different battery chemistries.
Redox Flow Batteries
Australia is one of the leaders in the development and deployment of different battery chemistries, particularly for grid storage applications. Several research institutions and companies are involved in the development and manufacturing of flow battery technologies, and a growing number of projects are in operation or under construction.
Some of these projects are helping to demonstrate the feasibility and benefits of flow battery technology and battery chemistries for a range of energy storage applications, while others are more mature and well established.
There are several types of flow batteries being developed in Australia, including:
- Zinc-bromine flow batteries;
- Vanadium redox flow batteries; and
- Iron flow batteries.
Overall, the supply chain for flow batteries in Australia relies significantly on imports of raw materials and components. However, the development of local sources of raw materials and the growth of battery chemistries is helping to reduce this reliance and is supporting the growth of the local supply chain.
Australia is one of the world’s largest producers of vanadium, zinc and iron – key materials used in flow batteries. As flow battery technology continues to grow in popularity and demand, there will be opportunities for Australia to expand the production of battery chemistries and supply the global market.
However, this will require significant investment in mining and processing infrastructure, as well as the development of new technologies to extract and process these materials efficiently and sustainably to meet the demands of the battery market.
Some Australian companies are already developing commercial-scale vanadium electrolyte manufacturing plants in Australia. Vanadium electrolyte is expensive to transport, making domestic manufacturing the most economical option to support the rollout of vanadium batteries throughout the country and meet increasing international demand from major vanadium battery manufacturers.
The development of recycling technologies for flow batteries in Australia is still in its early stages, but as the use of flow batteries grows, there is increasing interest in developing more sustainable and environmentally-friendly solutions for managing end-of-life batteries and also to recover and produce critical materials from processing by-products. Some Australian companies are already actively investing in research and development in this area.
The growth of flow battery technology in Australia is driven by the country’s abundant renewable energy resources and the need for reliable and flexible energy storage solutions to support the integration of renewables into the grid. With ongoing research and development and the deployment of large-scale projects, Australia is well-positioned to continue to be a leader in flow battery technology.
Lead acid batteries
Lead acid battery chemistry is well-established and various manufacturing and recycling avenues are operating within Australia. The recycling rate of such batteries is amazing, and, in part, this can be attributed to the bulkiness of the batteries, the network of roadside assistance services and recognition from the community on the harmfulness of lead-containing products. The success of recycling drives the ambition in other battery chemistries which often have their own nuances and challenges in recycling.
Lithium-ion batteries
Lithium-ion batteries are arguably the most significant of these battery chemistries. In recent times, they have provided opportunities to develop a homegrown additional manufacturing industry, and there is a big push for this to happen to leverage the minerals sector, a sector which Australia arguably leads, and there is an opportunity in-country to go from mineral to cell/battery. The scale of the required battery manufacturing and speed of setting up facilities is critical.
Considering the input minerals, Australia has vast reserves of almost all of the components that make up current generation lithium-ion batteries. Companies are already mining and exporting minerals or processed minerals for the battery industry. The desire from the mining industry and government is to move up the lithium-ion battery chain to produce refined reagents or electrodes.
The advantage of such endeavours is typically related to the expertise available, the opportunity of location with minerals, and excellent regulatory frameworks for environmental protocols and safety and access to a range of markets. The challenges are typically associated with aspects such as energy costs, perceived labour costs and regulatory hurdles, and remoteness of some sites. The question for industry and government is how to make such a transition for in-country processing of battery chemistries attractive and commercially viable.
The biggest advantage for in-country cell production is access to almost all raw minerals in the country.
How can lithium-ion batteries in Australia be further developed?
The natural extension to developing battery chemistries in Australia is the production of cells, and various firms are looking into doing this at a range of scales. With cell production in the country, this may drive processing and electrode fabrication in the country as the demand and need increases.
Considering supply chains for cell manufacture, the challenge, generally speaking, is not the raw materials, as is the case in many battery manufacturing countries, but the processing and cell manufacturing aspects.
Acquiring processed minerals and electrodes for battery chemistries is the challenge, and for miners, an opportunity to produce for in-country cell manufacturers is an attractive option to move into a larger part of the battery value chain, it might be the ideal testing ground for their development. For cell manufacturers, the reality might be the need to acquire process reagents offshore, develop electrode(s) in-house and make cells in-house, rather than acquiring electrodes from onshore manufacturers that in turn source minerals onshore.
Some companies are moving into the electrode manufacturing stage in-country that can support the local cell manufacturing companies. However, many of the electrode manufacturing companies are eyeing cell production in the future while cell manufacturing companies are tied or committed to technology not locally developed or sourced. Part of this is the nature of companies working in this space, start-up companies and small-to-medium enterprises. Therefore, there is a disconnection between finding local opportunities or players in the supply chain and being tied to larger agreements. Often, the larger or more established agreements lend themselves to more reliability and hence are more attractive to investors. There might be an opportunity for acute companies to work with in-country technology from the various parts of the battery component space to develop in-country cells with in-country inputs.
In addition, any in-country cell manufacturers need to consider their customers. For in-country customers, there is an excellent selection of companies that develop battery chemistries, including packs, battery management systems, and build battery packs in Australia. This is an excellent production target, but any in-country cell manufacturing needs to compete with cells manufactured elsewhere. The demand is there, and therefore, a reliable in-country source may compete well in such cases, especially when lead times are considered. Here is an opportunity for careful supply chain management to deliver cells rapidly to in-country and regional or international needs. Furthermore, the cells developed can be targeted for use with the range of Australia’s climate conditions.
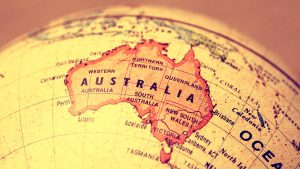
There are also in-country enterprises in the electric vehicle (scooter, bus) sector that can make use of these different battery chemistries. However, the lack of a large vehicle manufacturer can have an impact on production quantities. Again, as cell manufacturing develops, then once again a knock-on effect may see more interest in a larger battery pack or even further end product manufacturing in Australia.
Then we consider recycling. Australia is vast and battery recycling will be a challenge – particularly collection. The best solution may be a localised recycling system rather than a centralised site or drop-off points in targeted locations, such as electronics stores. Recycling companies are active in Australia, recovering batteries, discharging them, and separating components. The black mass is often shipped overseas for processing, similar to raw materials. However, as local electrode and cell manufacturing develops, a concomitant increase of onshore recycling may create relevant materials as inputs. Reusing and processing black mass or components in Australia could become feasible in the future.
Finally, it is worth noting that new or alternative battery chemistries can also provide opportunities which may play into the hands of the Australian battery sector. In particular, technologies that are pertinent to Australia’s climate and needs.
Recently, the Australian government requested feedback for the National Battery Strategy and the not-for-profit Australian Battery Society placed in a submission that encompasses some of the ideas presented above.
Please note, this article will also appear in the fourteenth edition of our quarterly publication.