Australia should develop into the downstream stages of the lithium supply chain to reduce criticality and capture more of its value.
The demand for lithium has greatly increased in the past decade with the shift towards renewable energies and electric vehicles, which require sophisticated battery storage technologies. It is estimated that 74% of the lithium used globally is for batteries (Fig. 1). The rapid increase in worldwide demand leads to an uncertainty of sufficient supply of lithium, and Australia is the world’s largest miner of lithium.
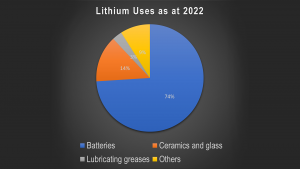
Australia’s reserves and resources of lithium
According the United States Geological Survey, lithium is approximately one-third as abundant in the Earth’s crust as copper and has a similar abundance to sodium. Australia’s probable and proven reserves are currently enough to supply 100% of the world’s current demand for up to 20 years. Australia has an estimated 6.2 million tons of lithium reserves out of an approximate 26 million tons worldwide, second to Chile with 9.3 million tons of lithium reserves.
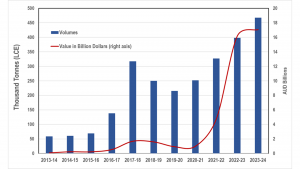
From these reserves, Australia currently produces 335,000 tonnes of lithium carbonate equivalent (LCE) and is expected to increase up to 470,000 by 2024 (Fig. 2). This is projected to provide over 40% of the world’s lithium demand of 1,091 tonnes of LCE by 2024. Although Australia is relatively well endowed with reserves and resources, the development of new mining capacity is constrained by the availability of capital and downstream processing.
The global lithium-ion battery industry chain
A mineral is considered critical if there is a risk of supply disruption for the mineral, and if the consequence of such a disruption would be great. Although the supply of lithium resources is not constrained, it is considered a critical mineral in that the majority of the downstream processing occurs in one country to produce battery technology (Fig. 3). China has a major contribution to the global refining and electrochemical stages with 89% and 75% respectively.
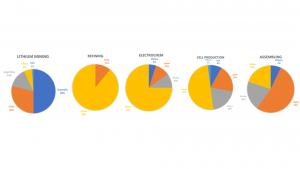
The lithium-ion battery industry chain can be divided into five main stages, namely:
1) Mining for materials;
2) Refining and processing;
3) Making battery materials;
4) Manufacturing the cells; and
5) Assembling the cells into battery packs.
The least value obtained is in the mining stage and the most value obtained is in the battery pack system assembly stage (Fig. 4). Australia earns less than 1% of the ultimate value of lithium-ion battery packs. Approximately, 99.5% of the value of lithium is added through offshore processing, cell production, and battery assembly.
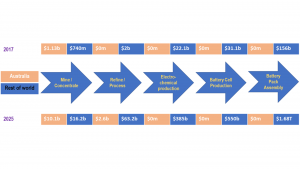
To capture more of the value of the lithium supply chain, Australia must seize more of this, for example, through downstream processing and the production of lithium-based chemicals. Locating processing facilities near to mines can provide a competitive advantage as well, with potential for a six-fold increase in efficiency in transport and logistics.
By building downstream processing capacity, Australia will not only un-constrain the development of lithium mines, but it will also increase Australia’s share of the supply chain, and reduce the world’s reliance on China for the refining stages.
Australia can move along the lithium battery supply chain
Australia will capture up to three times more value in the supply chain, if it expands into the second stage of the supply chain (refining and processing) and the following synergies will be realised:
- Transport efficiency: The lithium products that Australia ships contain 6% lithium and 94% waste. Building the processing facilities closer to the mine would result in over a six times increase in the transport efficiency.
- Academia and industry: A growing lithium processing industry, which will be supported by academia and the wider research sector, will lead to capabilities that are transferable to other minerals fields, including other critical minerals.
- Availability of chemical reagents: Australia already produces 13 out of 14 typical reagents and consumables which are the largest operational cost for refining plants.
The third stage of the supply chain involves the electrochemical production. If Australia builds industrial capacity in electrochemical production, it will:
- Capture substantial further value for our mineral resources. Australia produces all of the ten mineral elements required to produce lithium-ion battery electrodes, ranking first and second for global nickel and cobalt resources, respectively (Fig. 5).
- Further development synergies in academia and industry.
- Capture further value: Up to 20 times in the value captured compared to only mining for lithium.
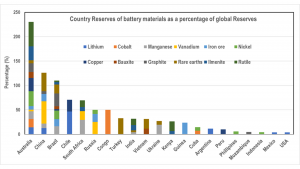
The cure to supply concentration is diversified and resilient supply chains. For example, Australia produces almost ~50% of the world’s lithium and the rest of the minerals required to produce lithium-ion batteries but the main constraint to mid-stream or downstream expansion seems to be the availability of capital, scale and/or technology, rather than a lack of ore. Australia is well placed to leverage its world-leading METS sector capabilities and tremendous mining technical knowhow by working with its international partners and allies.
Australia must develop into the downstream stages of the lithium supply chain to capture its value
The importance of lithium is due to 89% of the world’s lithium refining being done in China. This poses pressure in the supply chain as a disruption here would have great consequences. To combat this criticality, Australia, already a world leading lithium miner, should develop into downstream stages of the supply chain, in particular, refining and electrochemical production. This would not only reduce criticality, it will greatly increase Australia’s value captured from the lithium supply chain.
Mohan Yellishetty
Associate Professor
Co-Convener
National Industry Working Group (Critical Minerals)
Co-Founder
Critical Minerals Consortium
Civil Engineering
Monash University
David Whittle
Professor
Adjunct Professor (Practice) and Co-Founder
Critical Minerals Consortium
Civil Engineering
Monash University
https://www.monash.edu
Dr Roger Hu
Civil Engineering
Monash University
https://www.monash.edu/
Dr Mahdokht Shaibani
Lecturer
Chemical and Environmental
Engineering
RMIT University
https://www.rmit.edu.au/