Dr Mueller (DrM), Switzerland, manufactures innovative filters that can tackle large batch sizes and cell concentrations in the production of biologics.
As the biologics industry is moving towards more diverse batch volumes and cell concentrations that are cultivated in single-use facilities, there has been a demand for innovative cell separation technologies. Conventional technologies such as depth and cross-flow filters have limited flow rates, extremely large footprints, and rely on high filter areas. The latter causes a high amount of leachables and extractables, is unsustainable, and causes high investment and operating costs.1
The innovative CONTIBAC® SU filter developed by DrM, Dr Mueller AG in Switzerland overcomes these limitations by using a cyclic cake filtration method. Thanks to the cake filtration, this particular filter has an unequalled speed without sacrificing filtrate quality, and the cyclic operation allows for filtering the same batch volume with a smaller filter. This means that by using a smaller filter, not only is it more sustainable, but it also significantly reduces the risk of contamination.
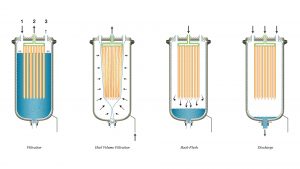
The working principle
The CONTIBAC® SU introduced in this study by DrM overcomes the limitations of current mammalian cell separation technologies by using two novel concepts:
- Cake Filtration: The filter media does not perform the actual filtration, but instead, it acts as a support for the filter cake consisting of cells and filter aid. As a result, the filtration is much faster, and the filter media can be regenerated by being back-flushed from the opposite side; and
- Cyclic Operation: Since the filter media can be regenerated, the filter can be operated in a cyclic manner that is illustrated in Fig. 1 (see above).
The working principle of a single filtration cycle is illustrated in Fig. 1. The filter is filled through connector one, and once filled, the liquid pushes through the filter media into the vertical elements and exits the filter through connector two. As the filtration is carried out, a cake forms on each element.
When the cake has grown to a degree that causes a significant drop in the flow rate, it then proceeds to the next step: the heel volume (HV) filtration. Air is pumped between the filter bag and the filter housing, squeezing all the remaining liquid out of the bag. In the subsequent step, the filter elements are back-flushed by pumping water for injection (WFI) or buffer through connector two. As a result, the cake is removed from the filter elements, and the filter media is regenerated for the next cycle. The filter cake accumulates as a slurry at the bottom of the bag and is discharged by opening the bottom pinch valve. Doing so regenerates the entire filter bag for the next cycle.
The advantage of using the aforementioned cyclic filtration technique is that a smaller filter size can be used to perform the same task. Unlike conventional filters, whose capacity is limited by the filter area, the capacity of the CONTIBAC® SU filter is only limited by the number of cycles, or respectively, the time the user has allotted for the filtration. A smaller filter also leads to a smaller footprint, a lower contact area (resulting in less leachables and extractables), as well as lower investment and operating costs.
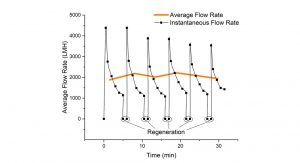
Case study
Suspension growing Chinese Hamster Ovary (CHO) DP-12 cells, producing an Immunoglobulin (IgG)-1 antibody against Interleukin-8 (clone #1934, ATCC CRL-12445, provided by Prof Dr T. Noll, Bielefeld University, Germany), were cultivated in a chemically defined medium. At the time of the harvest, the total and viable cell densities were 22.3 and 20.8 million cells per ml, respectively. The solids content was 49.3 g/L and the viability was 93.2%. The pH was reduced from 6.75 to five prior to the harvest by adding diluted acetic acid, and 40% Celpure® C300 filter aid was added per wet cell weight. The experiments were performed at a pressure of 1.5 bar with an FDA certified filter media having a nominal pore size of 0.9 µm.
The flow rates obtained over six cycles are shown in Fig. 2. In each cycle, the flow rate started high and decreased as the cake was growing. In conventional filtration systems, such as depth filters, the filtration is continued until the flow rates drop very low, at which point the filter is replaced. On the other hand, in the CONTIBAC® SU each filtration cycle is terminated once the flow rate drops significantly below the initial flow rate. In this case study, each cycle was terminated once the flow rate approached 1,000 LMH, at which point the filter was back-flushed, the filter media regenerated, and a new cycle was started.
After the back-flush, the flow rate went back to the initial level, and a high average flow rate of around 2,000 LMH could be maintained over all six cycles. Therefore, there was no sign of fouling or dip in the performance, something that cannot be achieved with conventional filters. Depth filters, for instance, cannot be back-flushed and even experience severe fouling within a single filtration cycle. Cross-flow filters require high flow speeds and thereby induce cell damage, which inevitably causes fouling. Unlike in these two technologies, the filter media in the CONTIBAC® SU does not perform the actual filtration, but instead acts as a cake support, thereby being less susceptible to fouling. Moreover, the pH reduction agglomerates impurities such as cell debris, DNA, and host cell proteins (HCP) and facilitates their separation from the liquid.3
The high performance of the CONTIBAC® SU does not come at the cost of filtrate quality. The filter reduced the turbidity by 98-99% and the amount of deoxyribonucleic acid (DNA) content by up to 90%. The activity of lactate dehydrogenase (LDH), a measure of the amount of cell damage, only roughly doubled, which is an outstanding result compared to competing technologies.3
Conclusion
The innovative filtration technology by DrM exhibits exceptional performance while producing high filtrate quality. High average flow rates in combination with cyclic operation allows for using smaller filters, which in turn reduces the investment and operating costs, decreases the footprint, and reduces the amount of leachables and extractables.
Moreover, the CONTIBAC® SU is highly suitable for larger batch volumes, higher cell concentrations and even continuous production, leading the biologics production into a brighter future.
References
- Lee, B., Langer, E., and Zheng, R. 2011. Next Generation Single-Use Bioreactor Technology and the Future of Biomanufacturing: A Summary from the Manufacturers and Users Perspective. Single-Use Technology in Biopharmaceutical Manufacture, Eibl R., Eibl D., Wiley-VCH Verlag GmbH, Weinheim, Germany, pp 183-194
- Moakler, B., Julkowski, K., and Dietiker, B. 2019 October 4. Multi-Cycle Single-Use Filter Optimizes Biopharma Processes. International Filtration News. Avialble at: https://www.filtnews.com/multi-cycle-single-use-filter-optimizes-biopharma-processes/
- Minow, B., Egner, F., and Jonas, F. et al. 2014. High-Cell-Density Clarification By Single-Use Diatomaceous Earth Filtration. BioProcesses International, 12(4), pp. 36-46
Tizian Bucher
Head of R&D
DrM, Dr. Mueller AG
+41 44 921 21 21
mailbox@drm.ch
www.drm-lifescience.com
Please note, this article will also appear in the first edition of our new quarterly publication.