Dr Joseph Zimmerman, a Senior Scientist at CU Aerospace, discusses recent experimental investigations of applications for low-temperature plasmas.
Solids, liquids, gases, and plasmas. As the world’s understanding of the fourth fundamental state of matter and complex plasmadynamics expands, new technologies are being invented to solve modern problems by utilising low-temperature plasma.
Various government-funded efforts have been focused on the development of low-temperature plasma low-temperature plasma devices. In recent years, small-business research opportunities have been guided toward converting various candidate low-temperature plasma technologies into marketable commercial and dual-use products. The aim has been to apply the fundamental plasma science knowledge base to create new applications. The outcome has been various novel approaches applying low-temperature plasma in ways that can lead to public benefits in industries such as aerospace, microelectronics, energy, and biomedicine.
Low-temperature plasmas can be generally defined as partially ionised plasmas that create chemically reactive environments in gases, on surfaces, and at interfaces with liquids. Due to the electron temperature being similar to threshold energies of electronically excited states in neutral atoms and molecules, power transfer from the electrons in low-temperature plasmas is efficient in the production of activated species, providing radicals, electronically excited states, and energetic photons, which can drive chemical processes.
In the past decade, advancements of low-temperature plasma have demonstrated commercial and technical value in various areas, including space propulsion, materials processing, healthcare technologies, agriculture and food storage, and chemical processing techniques. The continued advancement of innovative techniques and the integration of low-temperature plasma into various industry approaches offers exciting possibilities for improvements in performance, efficiency, and reliability, as well as enabling new product design spaces. Furthermore, there are numerous opportunities for synergistic advancements, as progress in one field of applications can lead to beneficial advancements in another.
CU Aerospace (CUA), located in Champaign, Illinois, USA, has been developing innovative low-temperature plasma technologies and devices aimed at various applications which may offer significant societal benefits. Recent CUA technology development efforts based on the Sterilizing Plasma Afterglow Reaction Chamber are overviewed herein, including approaches for plasma-based sterilisation, plasma flow control, and plasma-assisted combustion.
Plasma sterilisation using afterglow of oxygen-helium gas discharges
CUA’s technology, called the Sterilizing Plasma Afterglow Reaction Chamber (SPARC), is a new approach to the sterilisation of devices. The key advantages of this technology – compared to the state-of-the-art – are improved logistics of operation, reduced occupational risks, and low-temperature operation. CUA has developed this technology as both a means for sterilising medical devices, in work sponsored by the US Department of Energy, and more recently as a process for sterilising spacecraft and return sample surfaces for planetary contamination control, sponsored by NASA.
This approach is derived from CUA’s work with Electric Oxygen-Iodine Lasers (EOILs), an all-gas phase high-energy laser technology. In this laser system, radio-frequency (RF) discharges are applied to generate significant flow rates of singlet-delta oxygen, or O2(a1Δ), which is an electronically-excited state of oxygen gas. Each excited molecule stores 0.977 electron volts or 1.565×10-19 joules. This electronic-excited state has a long lifetime at low pressures, and so it can be used as an energy reservoir. For application in a high-energy laser, the exhaust from a flowing oxygen discharge, or plasma afterglow, is mixed with iodine and passed through a supersonic nozzle to cool the flow prior to entering a high-efficiency laser cavity. This results in the dissociation of molecular iodine by excited atoms and molecules in the plasma afterglow and the pumping of atomic iodine by resonant reactions with singlet-oxygen to create a population inversion (positive gain) and the extraction of laser power at 1315 nm (near-infrared).
In SPARC technology (see Fig. 1a), the electronically-excited oxygen plasma afterglow is instead used as a sterilant to attack and kill harmful pathogens on contaminated surfaces. This technology has already been demonstrated to remove various bacterial species deposited on cellulose nitrate filter papers, including E. coli K-12 (see Fig. 1c), Staphylococcus epidermidis, Geobacillus stearothermophilus spores, and Bacillus atrophaeus spores. Further work calls for the technique to be demonstrated on various surfaces and the development of a closed-cycle approach (see Fig. 1b).
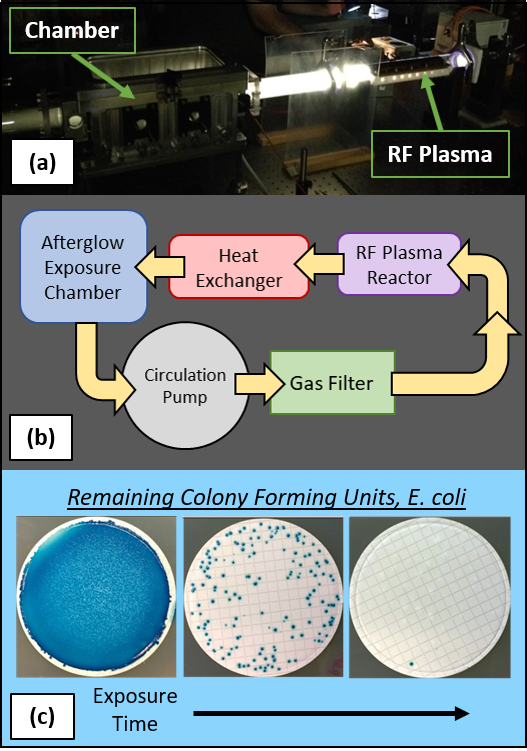
In addition to developing a closed-cycle SPARC apparatus, continuing work by CUA is aimed at developing an improved understanding of how effective this plasma afterglow approach is for inactivation of bacteria on various surfaces, including the compatibility of various aerospace and medical materials with the process for the exposure times required for effective sterilisation. There is also interest in exploring the use of in-situ resources to create plasma-generated reactive species, for example, drawing in atmospheric air or being able to operate in the Martian atmosphere (i.e., CO2).
Plasma flow control in aerospace applications
Numerous applications of low-temperature plasma exist in the aerospace field. This is because LTP can be applied to add energy to aerodynamic flows in various ways to impact fluid-dynamic behaviours or to modify chemistry in reacting flows. The application of low-temperature plasma to aerospace has resulted in various applications, including plasma flow control actuators embedded in aerodynamic surfaces, plasma-assisted combustion (or plasma-enhanced combustion) devices, and plasma-based thrusters in spacecraft. The applied novel plasma technologies fall into various categories, including microwave-excited, dielectric-barrier discharges, and gliding arc types. A key challenge is developing a plasma system that can be effectively integrated into the aerospace system, considering the impact of the plasma device on size, weight, and power.
One recent technology that CUA has developed in partnership with the University of Illinois at Urbana-Champaign (UIUC) is a novel device referred to as a Cyclotronic Arc Plasma Actuator (CAPA), which is intended as a mechanism for boundary layer flow control. This device operates by the breakdown of a plasma filament between two coaxial electrodes with a magnetic field placed transverse to the current path. Due to the drift motion across the magnetic field, charged particles in the plasma experience a Lorentz force, causing the arc to sweep about the centre of the coax. For the coaxial device pictured in Fig. 2a, having a magnet buried beneath a dielectric surface, a visible plasma disc is formed. When viewed with high-speed imaging, it is observed that this disc is really due to a rapidly moving arc filament (see Fig. 2b).
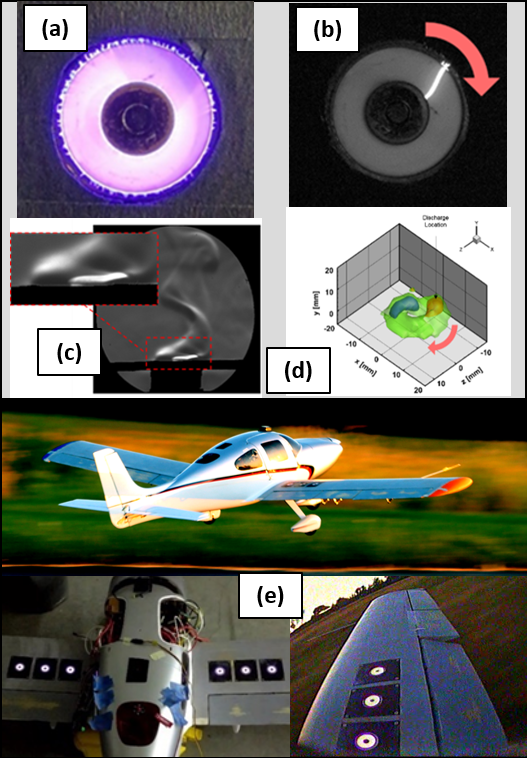
CUA and UIUC teamed up to further evaluate the flow fields associated with the CAPA device, applying both high-speed schlieren imaging and stereoscopic particle image velocimetry (stereo-PIV) techniques (see Fig. 2c and d, respectively). Further demonstrations led to integrating arrays of CAPAs into the wings of a UAV which was flight-tested to investigate the impact of this plasma actuator technique on dynamics during flight, and improved stall characteristics were demonstrated.
Practical household and industrial applications for low-temperature plasma
The development of the CAPA device for flow control in a UAV opens up new applications for this technology, leveraging similar compact electronics. While there are numerous technical challenges for applying this general approach to aerodynamic flow control, the lessons learned from this R&D can be leveraged for alternative applications involving chemistry. Recently, CUA was awarded a grant to study the application of this approach to plasma-assisted combustion. Simply put, the objective of this effort is to integrate plasma devices into practical burner systems, which can be applied in household and commercial applications such as tankless water heaters and industrial-scale burners.
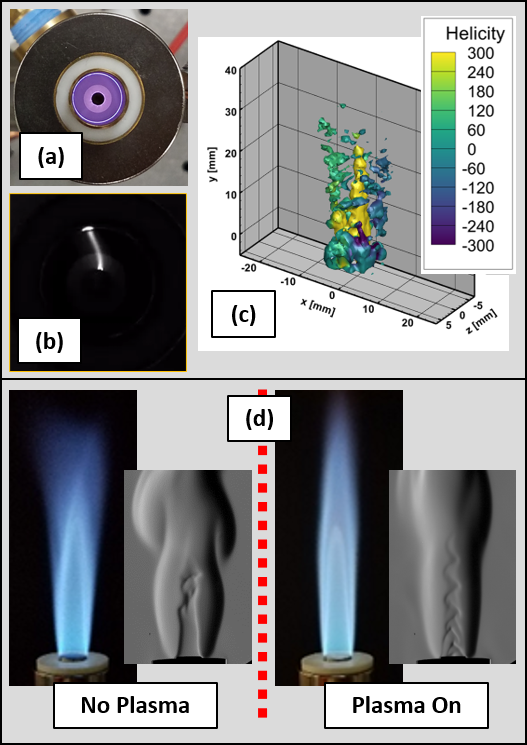
Fig. 3 shows various images of devices and experimental characterisation for Cyclotronic Arc Plasma-Assisted Combustors (CAPACs). In this application, the plasma filament is produced within a coaxial tube and used to excite premixed air and methane (or propane) flows. Applying similar diagnostics approaches to previous studies, CUA and UIUC teamed to show the impact that the plasma mechanism has on air-methane flames, which was well-characterised using stereo-PIV (see Fig. 3c) and schlieren (see Fig. 3d), including a significant 10x reduction in carbon-monoxide (CO) emission in fuel-lean operation. CUA envisions that this technique can be applied to provide efficient low-NOX fuel-lean operation, improved mixing and heat release and that it may also offer similar advantages for low-NOX operation with mixtures including hydrogen in natural gas infrastructure.