Moritz Hansen, Head of Marketing, Communication and Sustainability at Speira, discusses the importance of aluminium recycling and the company’s ambitious strategy that hopes to initiate a higher standard of sustainability within the industry.
As the transition to green energy becomes increasingly urgent, so too does the need for efficient and sustainable aluminium recycling. The production and subsequent recycling of metals, however, remains a significant contributor of CO2, which poses a problem for the development of net-zero batteries, construction and technologies such as electric vehicles (EVs).
Aluminium rolling and recycling company Speira recognises its importance in driving sustainable metal recycling and is at the forefront of devising net-zero recycling solutions. Capable of maintaining its properties while being infinitely recycled, aluminium has significant potential. Combined with its focus on decarbonisation, Speira’s aluminium production is not only pioneering but innovative as it develops a variety of solutions that can be widely applicable.
To discover more about Speira’s contribution to the green transition and the significance of aluminium recycling altogether, The Innovation Platform spoke with Moritz Hansen, Head of Marketing, Communication and Sustainability at Speira.
Can you tell us more about Speira as a company, its aluminium recycling objectives, and its journey to date?
Speira is a leading aluminium rolling and recycling company with an annual production of around one million tons of rolled aluminium solutions. We operate a total of 11 recycling and rolling production sites in Germany and Norway. These include our joint venture, Alunorf, the world’s largest aluminium casting and rolling plant, and Grevenbroich, our headquarters and the world’s largest aluminium refining plant. The European base is completed by our own research and development centre and our several sales offices across the continent. In total, Speira employs around 5,500 people in a wide variety of areas and functions.
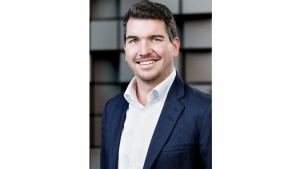
With over a century of experience and expertise in aluminium rolling and recycling, Speira supplies some of the best-known industrial companies in the global automotive, packaging, printing, engineering, building and construction industries. Our material solutions can be found in many everyday products, from beverage cans to tablet blister packs.
Our vision is to be a leading player and industry benchmark in sustainability. This approach is also reflected in our name. ‘Speira’ is Greek in origin and stands for a spiral of growing influence that grows from a strong core and inspires achievements. In addition, Speira represents the circularity of our business, where the processes of use and reuse are constantly repeated.
This year’s acquisition of the European business Real Alloy enabled us to significantly expand our recycling capacities and capabilities and take another important step towards decarbonising our business. The takeover included three aluminium and magnesium recycling plants in Germany, as well as an aluminium recycling plant and a salt slag recycling facility in Norway. The acquired recycling sites form the basis for Speira’s new Recycling Services business unit, enabling us to meet market demand for high-quality, low-carbon products. Speira now recycles up to 650,000 tons of aluminium per year, replacing primary aluminium with a high percentage of recycled metal. Therefore, Speira takes the number one position in the European aluminium recycling business.
How is Speira contributing to the road to net zero? What are the key decarbonisation pillars that the company is focused on?
Sustainability and connected decarbonisation are in clear focus at Speira, and we take a holistic approach. We are dedicated to protecting our planet in the best possible way, not only for us and our customers, but also for future generations. It is our ambition to work efficiently and conserve resources, which is why we committed to being fully decarbonised by 2045, five years earlier than the Paris Agreement targets. To achieve this goal, we are pursuing an ambitious sustainability strategy that will gradually reduce our emissions based on the targets set out by the Science Based Targets initiative.
The main pillars for reducing Scope 1 (direct) and Scope 2 (indirect) emissions are electrification and the use of alternative fuels, the use of renewable energy sources, and a continued focus on energy efficiency. With these three pillars, we can reduce 25% of Speira’s total CO2 emissions. Achieving net-zero Scope 3 (value chain) emissions is based on growth in aluminium recycling, a strong focus on sourcing low-carbon metals, and further development of recycling-friendly alloys. Through responsible sourcing of metals and raw materials, combined with increasing use of scrap, we are able to save 75% of Speira’s total CO2 emissions. By carefully selecting our metal suppliers, we have already reduced our CO2 emissions by 25% in the last five years and, by 2025, the use of recycled metal in our production will exceed 40%.
Our responsibility goes beyond the manufacturing of our rolled products. Speira is actively engaged in closing material loops and supports various initiatives to ensure that even more aluminium products are properly recycled after their first life cycle. Our sustainable commitments and production sites are regularly audited and certified by external organisations. Speira is also a member of the Aluminium Stewardship Initiative (ASI), where human rights, resource reduction and employee wellbeing are part of our certification, according to the ASI Performance & Chain of Custody Standards.
What e-mobility solutions does Speira offer?
In addition to rolled aluminium products for interior and exterior vehicle applications, Speira offers a broad portfolio of reliable solutions for the e-mobility sector. As a solid material with high thermal conductivity and the ability to be formed into complex shapes, aluminium recycling is ideally suited to this application. With our semi-finished products, we link sustainability and mobility.
Speira’s portfolio includes a variety of solutions for use in bodyshells, battery boxes and contact systems. Our products for cell and module housings combine high safety, significant weight savings and excellent thermal conductivity. They protect high-performance batteries not only in the event of a crash, but also against corrosion. Our materials for battery boxes meet all requirements for electromagnetic compatibility (EMC), as well as water and gas tightness. The alloys used in our battery boxes are also weldable and can be formed for complex geometries and precisely fitting solutions. In connection with busbars, our materials enable the balancing act between high specific conductivity, lightweight potential, and low contact resistance. Compared to copper, aluminium is significantly more cost efficient.
Our specially developed materials for heat exchangers in battery applications guarantee sophisticated and efficient thermal management. A more homogeneous temperature distribution in the cell optimises performance and increases durability. Efficient cooling of the entire battery system also enables faster charging. Thanks to excellent formability, bonding, solderability, and easy further processing, our materials enable tailored solutions for every application.
Speira’s battery electrode foil serves as a carrier material for the active mass of a lithium-ion battery and is available in various thicknesses. In addition to excellent conductivity, it has high flatness values and low porosity. Maintenance of the highest quality requirements mean our products meet the demanding automotive standards and are certified according to IATF.
Why is aluminium a crucial component for battery solutions?
Aluminium is an extremely versatile material whose properties make it essential in battery technology. In addition to its low weight and high formability, aluminium has excellent electrical and thermal conductivity. The material not only combines safety with lightweight construction, it can also improve battery performance. As a key enabler of excellent thermal management, aluminium provides more efficient cooling of the battery system, faster charging, and even longer battery life. Moreover, the use of aluminium is sustainable, as the material can be infinitely recycled without losing its properties. Sustainable aluminium recycling can make a significant contribution to meeting future CO2 emission reduction requirements while enabling the circular economy.
At Speira, we have long recognised the potential of aluminium in the battery environment and started early to develop alloys that meet our customers’ requirements. Through proper alloying and intelligent process control, we have been able to optimise the range of positive product properties and significantly drive the market forward. Our experience makes us a reliable development partner for battery technology and customised product solutions.
As an aluminium rolling and recycling company, we are convinced that the battery sector will grow and continue to offer many opportunities for innovation. Speira has an extensive product portfolio and is already a volume supplier to the world’s leading battery manufacturers. As described above, our ION product family covers the entire range from battery electrode foil to cell connectors, heat exchangers and housing materials.
What is the role and potential of aluminium recycling in Europe’s green transition?
Aluminium recycling plays a vital role in the transition to a more sustainable energy system and a greener, more circular economy. From wind and solar power to alternative fuel cells, hydrogen production, high-voltage transmission lines, and batteries, aluminium is used in nearly every energy generation, transmission, and storage technology. The European Commission’s study ‘Critical raw materials for strategic technologies and sectors in the EU’ demonstrates that aluminium is one of the most significant materials in the green transition. Global demand is projected to increase by 50% by 2050.
Today, aluminium production is responsible for 2% of global CO2 emissions. Energy consumption and greenhouse gas emissions from the aluminium industry will likely continue to increase due to rising demand for aluminium. However, if we fully leverage the potential of recycling, source raw materials sustainably and ensure a green energy mix, the material has the potential to become a net contributor to climate protection.
When it comes to sustainable aluminium recycling, the carbon footprint of the European primary production process is much lower than the global average, with only 6.8kg of CO2 emissions compared to the worldwide average of 17kg CO2 per kg of aluminium produced. At Speira, the carbon footprint of our aluminium products in 2022 was 5.8kg CO2 per kg of aluminium. These figures highlight the importance of location in aluminium production to ensure CO2 emissions are low. Here, political framework conditions play a significant role in ensuring the competitiveness of the European aluminium industry and thus enabling sustainable production of aluminium.
Please note, this article will also appear in the fifteenth edition of our quarterly publication.