Technological development can boost lithium production, avoid energy use and emissions, and provide control in the lithium value chain. Max Luedtke, Global Business Line Manager Mining, and Eduardo Lima, Global Solutions Architect at ABB, explain.
Lithium has become one of the world’s most precious commodities in just a few decades. It is a critical component in everything from electric vehicles (EVs) to smartphones – and a driving force behind the global energy transition from fossil fuels to renewables such as solar photovoltaic (PV) and wind.
Until the mid-2010s, for most minerals, the energy sector represented a small part of total demand. According to the International Energy Agency (IEA), in a scenario that meets the goals of the 2015 Paris Agreement (the IEA Sustainable Development Scenario), clean energy technologies’ share of total lithium demand increases over the next two decades to almost 90%. EVs and battery storage have already displaced consumer electronics to become the largest applications for the metal.
This shift has profound economic and geopolitical implications around price volatility and security of supply, not to mention reducing emissions of greenhouse gases (GHGs) during lithium production.
Wind farms and EVs often require more minerals to build than their fossil fuel based counterparts. A typical electric car requires six times the mineral inputs of a conventional car, and an onshore wind plant needs nine times more mineral resources than a gas-fired plant. Since 2010, the average amount of minerals required for a new unit of power generation capacity has risen by 50%.
In addition, as intermittent energy sources like solar PV and wind continue to grow their share in the overall energy mix, so the need to supply mines with continuous clean electricity using innovations such as power microgrids and battery energy storage systems (BESS) becomes ever more critical.
This article will discuss what this means for mine operators and specialist technology companies that design automation and electrification technologies. Through industry collaborations and contracts, these companies help to optimise lithium production and profitability, avoid GHG emissions, downtime and costs, and facilitate a new approach to power provision that relies on a holistic view of the entire mine energy ecosystem.
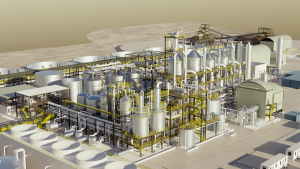
De-risking and optimising lithium production
To improve methods of lithium extraction, ABB believes collaboration with technology providers, OEMs and mine operators at the earliest possible stage in the mine life cycle is the best way to de-risk process plant development, improve efficiency, reduce energy use and emissions, and save on capital expenditure and operating expenditure (OPEX).
The company then uses electrification and automation technologies, and those of its partners, to deliver a solution architecture across the entire value chain, encompassing the hardware and software stack, visualisation and analytics tools, and operations: Electrification, maintenance, processing and sustainability.
Let’s take, as an example, the Ioneer Ltd. lithium-boron deposit being developed at the Rhyolite Ridge Lithium-Boron Project in Nevada, US, where ABB is managing process automation, power management and electrical distribution for our Australian-listed customer. ABB is providing its integrated automation and electrification solutions, including site services, to drive optimisation and digital transformation of the mine’s processing plants from the outset.
The site, with the only known lithium-boron deposit in North America and one of only two such deposits in the world, is considered to be globally significant. It requires specific systems engineering and optimisation technologies and expertise. ABB’s package includes plant-wide process automation and instrumentation systems for the power generation, acid, and lithium-boron processing plants. ABB’s involvement supports ioneer’s move towards long-life, cost-effective sources of lithium and boron that are vital for the global energy transition.
This holistic approach, whereby a single vendor provides a portfolio of solutions – from the steam turbine generator and medium and low-voltage electrical distribution to power management and process automation – offers the client an overview of the entire ecosystem rather than separate automation, electrification and instrumentation packages from multiple technology suppliers.
The ABB Ability™ System 800xA distributed control system (DCS) orchestrates power and process control and a high-integrity safety system. The latter is particularly important in the chemical processing of lithium. Using System 800xA to optimise power generation is a real differentiator in that many mines employ cogeneration, meaning they generate their own steam. Using the platform, customers can reuse this steam to generate power, optimising operational performance and long-term OPEX.
Integrated power management and storage
Lithium operations are often situated in remote locations far from established infrastructure and power grid systems. Limiting the environmental impact of these types of mines is exacerbated by the fact that extractive projects are becoming more energy-intensive, with 60–70 MW operations the norm rather than the exception.
Again, engaging with a trusted technology supplier at the earliest possible stage of both greenfield and retrofit mine power projects is essential to ensure the external grid is robust enough to transfer sufficient quantities of power 24/7 and that the internal network addresses the specific operational demands of the mine, from hoisting and grinding to hauling and material handling.
The challenge for technology providers is to develop solutions integrating renewables with power management and storage systems to provide stable power distribution. For example, ABB customers may have a diesel generator that powers an on-site data centre and servers. Replacing this with a UPS (uninterruptible power supply) and battery storage system has the dual benefit of avoiding GHG emissions from the enterprise while simultaneously ensuring the all-important security of supply.
Decarbonising lithium production from pit to port – and onwards throughout the entire lithium-ion battery value chain – begins with the electricity transformation of off-grid mining to BESS and renewable sources of electricity. Many progressive mining companies are also investing in fully electric or hybrid-electric vehicles and trolley systems to cut diesel usage, costs, and pollution.
At Boliden’s Aitik copper mine in northern Sweden, the DCS acts as an OT platform connecting multiple aspects of the operation. By expanding System 800xA from the processing plant to the mine itself – and integrating both into a single platform – ABB can connect haul truck trolley systems to the same automated platform that runs the enterprise, part of a trend towards hardware or control systems that handle all the on-site power generation, including renewables integration and off-grid storage.
Case studies: Australia and Chile
To cater to this new reality, ABB provides powertrains for mine vehicles and equipment, battery storage, modular battery containers, and independent microgrid solutions. In this sense, the company is adopting more of a power management role, providing services such as recessionary energy storage, power behaviour modelling, and reliable grid connection.
ABB’s eMine™ portfolio is designed to facilitate the transition to all-electric mines by integrating electrification and automation technologies to optimise everything from grinding to vehicles to conveyors – resulting in more efficient, sustainable energy and resource consumption.
In the US, ABB is engaged with an Australian company that is establishing and operating a greenfield lithium mine and chemical plant. This is another example of how early project engagement enables ABB to tailor and integrate automation, electrification, and instrumentation solutions, as well as execute engineering work to optimise the various packages. Meanwhile, in Chile, the company is working on a brownfield lithium brine project, supplying automation solutions for process control.
Geographically, many countries not only want to mine lithium but also establish a connected battery production chain, including gigafactories, an example being ABB’s collaboration with Northvolt in Sweden. So, the role of the technology vendor is also changing in another way, in that it is no longer just about providing specific technology products to a single customer, but developing solutions for the entire lithium value chain, from miners to chemical processors and automobile manufacturers.
A change of mindset
In conclusion, the energy transition from fossil fuels to renewables continues and necessitates not only new technology solutions but also new mindsets and ways of working, both from mining companies and technology specialists. Mine stakeholders and shareholders are pushing companies to look after sustainability on greenfield and brownfield sites using innovations such as advanced process control.
Until relatively recently, many mining companies were happy to keep automation to a minimum, as long as they continued to hit their key performance indicators for production. Now, sustainability and digitalisation are key, specifically how automation and electrification can be deployed to reduce their carbon footprint.
Technology is the enabler of this change. The mining sector is becoming less risk averse, particularly in the lithium space, as junior mining companies with a more agile mindset enter the market. In this sense, the energy and technology transition must be supported by the transformation of processes, people, and culture to attract a new generation of environmentally aware, digitally literate talent, ensuring that reserves of lithium for Li-ion batteries are mined efficiently, safely, and sustainably.
As we have mentioned, partnering with a specialist technology vendor at the earliest possible stage in the project life cycle is critical to ensure that automation, electrical, and instrumentation solutions not only take into account the needs of the individual mine, but also encompass the entire mine life cycle, from pit to port. This will not only help reduce emissions and energy use, but also help build the sustainable lithium supply chains of the future, ensuring that this critical resource can fulfil its vital role in the energy transition, and contribute to a safer, cleaner world for future generations.
Please note, this article will also appear in the seventeenth edition of our quarterly publication.