Adionics’ ambition is to industrialise its clean and sustainable solution for direct lithium extraction from brines, enabling the electric mobility chain to develop virtuously.
The decarbonisation of economies is a major challenge. Transport, responsible for 27% of greenhouse gas (GHG) emissions, must shift towards clean mobility, particularly electric. Forecasts for the development of electric vehicles (EV) are therefore fundamental in predicting the demand for lithium. Depending on the situation, the percentage of electric vehicles could represent between 30-50% of the total number of vehicles in 2050.
Lithium’s role in the EV transition
Lithium production is therefore essential to meet the growing demand for EV battery manufacturers. The demand for lithium, including lithium hydroxide and lithium carbonate, is exploding due to the emergence of electric mobility. Lithium carbonate demand is forecasted to grow by 23% per year, while lithium hydroxide could grow by 33% per year.
Today, more than 50% of lithium production is used for EV batteries, which could jump to 80-90% by 2030. The explosion in demand for electric vehicles worldwide, and particularly in Europe, suggests that we will face a strong decorrelation between supply and demand. Between 2019 and 2021, lithium demand increased by 170%. Projections foresee a demand of over two million tons of lithium carbonate by 2030, equivalent to a fivefold increase.
The lithium resources make it possible to meet the needs without major difficulties. These resources are concentrated in South America (the famous Lithium Triangle comprising Bolivia, Argentina, and Chile), but significant resources also exist in the United States, Australia, the Democratic Republic of the Congo, Germany, Canada, Mexico, and China.
Between 2016 and 2019, spodumene lithium (mineral of the class of silicates containing lithium) gained market share due to shorter development time and the ability to produce battery-grade lithium hydroxide (LiOH). However, it is important to note that rock lithium mining generates inhalable and respirable dust particles.
The transportation, storage, crushing and processing of ore involve very high energy consumption. Finally, spodumene, which is very insoluble in water, requires large volumes of dilute acids (as sulphuric acid) to dissolve the hard rock and leach the crude lithium mineral compounds. The rock mines (spodumene, petalite, etc.) currently produce the largest quantity of LiOH at the most competitive price in the world.
LiOH from spodumene produces the most CO2, while lithium carbonate or hydroxide production from brine has the lowest carbon footprint.
From an environmental point of view, it is therefore necessary to support the growth of lithium from brine to significantly reduce carbon footprint. The Latin American Brine Lithium Triangle represents 70% of world reserves.
Direct lithium extraction from brines
To achieve direct lithium extraction from brines, today, state-of-the-art technologies used are the solar evaporation ponds, based on the evaporation of water and the fractional crystallisation of different salts present in natural deposits that are notably rich in lithium. This technique has some challenges, including long production time, low lithium yield recovery, huge water consumption and use of chemical reagents.
Depending on the brine composition and salar location, production recovery and lithium purity will strongly vary. Typically, with solar evaporation, lithium recovery cannot go higher than 50%. After successive evaporations, the brine highly concentrated in lithium must go through several post processing steps, costly in chemical reagents, to reduce remaining impurities such as boron, magnesium, and calcium.
Lithium brine producers need to adopt innovative salt extraction solutions to recover more value from their brine by increasing lithium yield. Reaching a much higher purity while reducing costly post processing steps, resulting in operating expenses (OPEX), is another challenge faced to enter the LiOH (lithium hydroxide) market and compete with spodumene LiOH.
The lithium sector is therefore faced with the difficulty of accelerating its production. Adionics, through its ambition and technology, aims to bring to the market the ability to accelerate direct lithium extraction from brines with much better yield (above 90%) and a very high purity, allowing access to the quality required for battery-grade production and therefore reducing the purification needs required with conventional methods.
The Adionics disruptive Direct Lithium Extraction (DLE) process: The Thermal Swing Salt Absorption (TSSA)
Adionics offers a unique and disruptive, efficient, sustainable liquid-liquid extraction and stripping solution of lithium chloride in a closed loop.
The project is based on ten years of R&D for salts extraction from brines, applied first to the desalination of seawater and then to the extraction of lithium salts, since 2017.
Adionics has developed a dedicated continuous flow liquid-liquid extraction process and a highly selective liquid extraction formula (the Flionex®) for lithium salts. This remarkable affinity for lithium allows us to strongly reduce the purification steps before conversion into lithium carbonate or lithium hydroxide (no extraction of boron, magnesium, potassium, sulphates).
The closed-loop process, which involves the liquid-liquid lithium extraction at ambient temperature and a stripping with a low flow of freshwater at higher temperature to produce a concentrated and pure lithium brine, is unique and patented by Adionics. Its high selectivity for lithium allows access to carbonation directly at the process outlet, making it possible to produce battery-grade Li2CO3 (lithium carbonate) without any further purification. In addition, the low level of impurities (sodium or calcium) in the lithium-chloride-produced solution allows access to finished products with very high added value, such as lithium hydroxide monohydrate or lithium metal.
Over the years, in parallel to R&D on our media and process, and to laboratory tests, Adionics has designed a mathematical model capable of forecasting lithium yield, purity and first estimations of capital expenditures (CAPEX) and OPEX for a DLE commercial plant. The simulator has been validated by numerous laboratory experiments.
We have tested our process and Flionex® on more than 50 different salar and geothermal brines, including those from Argentina, Chile, Europe, and the United States. The continuous flow tests are operated in Adionics’ process laboratory in the headquarters near Paris. Today, along with Adionics’ synthesis lab and analysis lab, the continuous flow pilot laboratory (referred to as the Clean Lithium 1) is operating with a capacity of one ton per year LCE and has repeatedly demonstrated the announced performance on lithium extraction.
Best-in-class solution for the lithium market
The technology, thanks to the high purity of the outgoing flow of lithium chloride (LiCl), will pave the way for direct conversion into LiOH in a more virtuous way for the environment (limited freshwater consumption, low electrical and thermal consumption, no chemical reagent).
Adionics technology contributes to the Sustainable Development Goals in several ways. The technology helps to gain three years to reach nominal production, compared to conventional lithium production from salars. It is a critical point to meet the strong demand from manufacturers of batteries using lithium. Brine consumption is limited in Adionics’ process – up to 100 times less freshwater consumption; completed by a better resource exploitation. Adionics’ Thermal Swing Salt Absorption DLE technology will open the possibility to re-inject or re-infiltrate the depleted brine, avoiding underground brine reservoir depletion compared to classical methods by evaporation.
Another important aspect is reduced electrical and thermal consumption. This also results in a reduction CAPEX and OPEX of up to -40%, to produce lithium carbonate or hydroxide from brine that opens competition with the spodumene mine (rocks). The Adionics process requires no chemical reagents to extract or strip lithium and has an extremely limited environmental impact, making this type of mining accepted by local communities.
Our technology makes it possible to achieve a lithium recovery yield of more than 90% from natural lithium brines against 50% with the conventional evaporation methods. Furthermore, Adionics technology unlocks access to raw brines rich in magnesium and sulphates (from Bolivia and Argentina, for example) and not exploitable by the usual technologies. It is also important to note that Adionics addresses all projects of lithium production, whether capacity increases using existing solar ponds or new projects with no impact related to the impurities contained in the brines (magnesium or sulphates, for example).
Pre-industrial phase and commercialisation
2022 is the preindustrial year for Adionics. By mid-2022, Adionics will count three new plants to work with clients. The Clean Lithium 15 is a demo plant with a capacity of 15 tons of lithium chloride production per year, and is located in Europe in a partner premises with the capability to test the full chain of value from raw brine to processed lithium chloride from Adionics Thermal Swing Salt Absorption (TSSA) and to the final product: lithium carbonate or lithium hydroxide.
The second demo plant will be like the first one, with the aim to be implemented in Latin America for long-test, in-situ conditions (salars). In May, the first preindustrial plant with a capacity of 250 tons of lithium chloride per year will be commissioned. The Clean Lithium 250 preindustrial plant will be accessible to evaluate the Adionics technology in real conditions with high flowrate of brines (1-3 m3/h).
The pre-industrial plant ‘Clean Lithium’ aims to develop a clean, efficient, and sustainable solution for the direct extraction of lithium from brines so that the chain of electric mobility develops on a virtuous basis.
The growing interest in our pre-industrial Clean Lithium plant, driven by our commercial efforts, will lay the groundwork for commercial plant discussions with our customers. The success of the implementation and in-situ production tests of our Clean Lithium pre-industrial demonstrator (250t LCE/year) is key to the success of the commercial units (25,000t LCE/year) in the coming years.
Adionics positioning
Adionics will contribute to accelerating world lithium production to match a very fast-growing demand. Primary objectives are to maximise, in a sustainable way, lithium recovery from brine with the highest purity to unlock access to battery-grade lithium carbonate and lithium hydroxide directly from our high purity output lithium chloride.
Adionics aims to meet the strong demand for lithium by offering stable production, qualitative and quantitative reliability, and sustainable assurance. Adionics technology addresses many of the above challenges by providing the market with the technology with low energy consumption, low consumption of fresh water, reinjection of lithium-depleted brine at the end of the process, no chemicals needed throughout the process, and no modification of brine pH.
As a result, Adionics TSSA presents a very competitive CAPEX/OPEX to lower the overall cost of operations (up to 40% compared to traditional methods). It also has a yield and purity of up to 99%, which gives direct access to the quality necessary for batteries of lithium carbonate and lithium hydroxide.
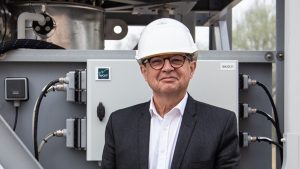
Adionics has already built two pilot demonstration plants for this process. The company’s Technology Readiness Level (TRL) in 2021 is 7 and is set to reach TRL 8 in 2022.
Adionics’ solution is addressed to naturally lithium-rich brine sources, such as salars, geothermal waters, and water produced in oil and gas. Adionics is also developing its technology to be applied to secondary sources to address the growing need in lithium batteries recycling.
Please note, this article will also appear in the tenth edition of our quarterly publication