Innovative calorimetric methods can improve the thermal management and safety of lithium and post-lithium batteries.
The European Commission has recently announced their approval of €3.2bn public support by seven Member States for a pan-European research and innovation project in all segments of the battery value chain. The project supports the development of highly innovative and sustainable technologies for lithium-ion batteries (liquid electrolyte and solid state). The safety of these innovations can be guaranteed by starting right from the beginning with thermal and detailed safety studies on the small-scale cell level in order to achieve in-depth understanding of the underlying reaction mechanisms and heat conduction processes, which are at the moment not known for post-lithium cells. Then the scale-up process needs to be accompanied by both thermal investigations and safety tests (thermal runaway, overcharging, internal/external short circuit, mechanical impact) in Battery Calorimeters of larger sizes. Established in 2011, the IAM-AWP Calorimeter Center operates Europe’s largest Battery Calorimeter Laboratory. It provides six Accelerating Rate Calorimeters (ARCs, Thermal Hazard Technology) of different sizes – from coin to large pouch or prismatic automotive format – which allow the evaluation of thermodynamic, thermal and safety data for lithium and post-lithium cells on material, cell and pack level under quasiadiabatic and isoperibolic environments for both normal and abuse conditions (thermal, electrical, mechanical). In addition, it offers sophisticated differential scanning calorimeters (DSC), thermogravimetric analysers (TGA), laser flash analysers (LFA) and extremely sensible Tian-Calvet calorimeters (C80, MS80, Setaram Instrumentation), which provide thermodynamic parameters such as heat capacity, thermal conductivity or formation enthalpy on the materials level. With these facilities, and the established technical and methodological expertise, the IAM-AWP is now seen worldwide as one of the few institutions that investigate both the thermodynamics and the safety of batteries and their materials.
The internal pressure is an important parameter, because its increase can be used as an early warning signal for thermal events that later might lead to the thermal runaway. Therefore, an innovative calorimetric method for the measurement of internal cell pressures has been established on 18650 cells and has recently been transferred to pouch and hard-case prismatic automotive cell formats.
A pressure line connected to a pressure transducer is directly inserted into the cell. Then the cell is sealed again with epoxy resin and the cell is placed into the calorimeter chamber, which has heaters and thermocouples located in lid, bottom and side wall. Finally, the internal pressure is measured during the thermal abuse test. The next step would be to develop a pressure sensor that could be integrated into the Battery Management System (BMS) to act as an additional safety feature.
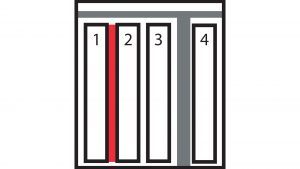
It is clear that safety issues have a major influence on consumers’ willingness to adopt new battery technologies, because an uncontrollable increase in temperature of the entire system (so-called thermal runaway) can cause an ignition or even explosion of the battery with simultaneous release of toxic gases. If it is not possible to stop a single cell from going into the thermal runaway, the last step is to prevent the propagation of the thermal runaway from one cell to the neighbouring cells, the so-called thermal propagation, or at least extend the time until thermal propagation to 5-10 min. This should give the passengers in an electric vehicle enough time to escape or to be rescued by the firefighters. The large-scale ARCs are well suited for studying thermal propagation. Recently at the Calorimeter Center a setup has been developed, which allows to develop and qualify suitable countermeasures, such as heat shields. This setup consists of metal box with a lid, which mimics a battery box and is put into the calorimeter chamber. Four pouch cells are installed in the box and equipped with thermocouples that are connected to the ARC software. A heater mat is attached to cell 2 and the heat shield material to be tested is installed between cells 3 and 4 and below the lid (see Fig.1). With the help of the heater mat, cell 2 is now heated up to initiate its thermal runaway and the time is measured until the thermal propagation reaches cell 4 (see Fig.2).
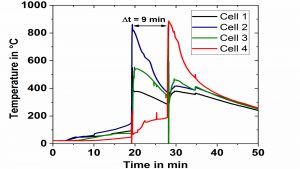
In late 2018, the POLiS (Post Lithium Storage) Cluster of Excellence was acquired jointly by KIT and Ulm university within the highly competitive Excellence Strategy competition of the federation and the federal states. It has a budget of about €7m per year and is scheduled for a duration of seven years. In this cluster the IAM-AWP Calorimeter Center is responsible for the field of thermal characterisation and safety of post-lithium electrodes and cells and will help pave the way for mature and safe sodium, magnesium or calcium batteries. In terms of future battery innovation, the main innovations will be either the development of powerful post-lithium batteries, or the introduction of solid-state electrolytes. The first approach will use more abundant materials instead of Li, Ni and Co. The latter will increase the safety level and enable the application of metal anodes that offer higher energy densities. The development of safe cells is of outmost importance for a breakthrough of the electrification of transport and for stationary storage. The specific materials design influences heat generation and heat dissipation during operation of the cells. Calorimetry of the cells, and their individual active materials is thus required to obtain quantitative thermal and thermodynamic data and for a holistic safety assessment the winning post-Li technologies will win partly on their safety argument, possibly sacrificing some energy density.
To summarise, battery calorimetry is now well established and is increasingly becoming more requested by our European research partners from both industry and academia, because quantitative and system relevant data for temperature, heat and pressure development of materials and cells are provided as a fast feedback for the cell developers and as input data for modeling and simulation. Thus, on the one hand, there are many requests from automotive OEMs and TIER1 suppliers for safety tests, and on the other hand there are more and more invitations to participate in public funded projects (such as the Horizon 2020 projects). There are still numerous challenges to address and we hope that our Calorimeter Center will help the European industry to make further progress in the battery field, which is urgently needed to reach a low-carbon future, to foster European leadership, and to create new jobs, which are the main objectives of the European Battery Alliance.
Dr Carlos Ziebert
Group Leader
Batteries – Calorimetry and Safety
Karlsruhe Institute of Technology
Institute of Applied Materials – Applied Materials Physics
+49 721 608 22919
www.kit.edu
carlos.ziebert@kit.edu
Please note, this article will also appear in the first edition of our new quarterly publication. Subscribe to our updates for free here.